Post by jiniya123 on Jan 5, 2024 23:45:44 GMT -6
Atunnel is a storage system for palletized goods that: Optimize storage space: They make full use of space by compressing goods stored on the upper floors and creating a corridor on the ground floor for order preparation. Improved picking performance: Picking is facilitated because operators simply walk down the aisle to pick the products that make up the order. Improved distribution of merchandise: They limit the number of operator moves by including within the same space a picking area and an area for stocking merchandise used when preparing orders. However, picking tunnels may not be sufficient to optimize performance in warehouses with high order preparation requirements.
In this case, it is recommended to replace manual storage systems with robotic solutions to increase productivity. For example, installing a pallet stacker guarantees an uninterrupted flow of goods to the picking area, thanks to a "product-to-person" system, in which robots automatically move the required products to the Graphics Design Service operator's location. installation of aisles on the lower level to facilitate order picking installation of aisles on the lower level to facilitate order picking Pick tunnel configuration The configuration of the compacted storage system allows for multiple combinations of storage of reserve pallets on the upper level and picking at ground level. Here are the most common configurations combining pallet storage with picking tunnels: Flexible racking: Pallets are loaded through one channel and unloaded through another channel with the help of the inclination and gravity of the channel.
This system is ideal for maintaining rotation as items are stored according to FIFO criteria, i.e. the first pallet that comes in is the first to leave. Push-back racking: Pallets are positioned and retrieved along the same aisle, which allows the last-in-first-out principle to be applied, i.e. the last products to enter are the first to leave. Pallet shuttle system: Pallets are loaded and unloaded through the same aisle, while electric carts move products within storage aisles, simplifying retrieval and positioning operations.
In this case, it is recommended to replace manual storage systems with robotic solutions to increase productivity. For example, installing a pallet stacker guarantees an uninterrupted flow of goods to the picking area, thanks to a "product-to-person" system, in which robots automatically move the required products to the Graphics Design Service operator's location. installation of aisles on the lower level to facilitate order picking installation of aisles on the lower level to facilitate order picking Pick tunnel configuration The configuration of the compacted storage system allows for multiple combinations of storage of reserve pallets on the upper level and picking at ground level. Here are the most common configurations combining pallet storage with picking tunnels: Flexible racking: Pallets are loaded through one channel and unloaded through another channel with the help of the inclination and gravity of the channel.
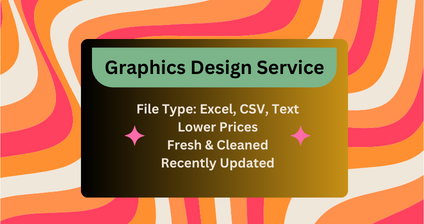
This system is ideal for maintaining rotation as items are stored according to FIFO criteria, i.e. the first pallet that comes in is the first to leave. Push-back racking: Pallets are positioned and retrieved along the same aisle, which allows the last-in-first-out principle to be applied, i.e. the last products to enter are the first to leave. Pallet shuttle system: Pallets are loaded and unloaded through the same aisle, while electric carts move products within storage aisles, simplifying retrieval and positioning operations.